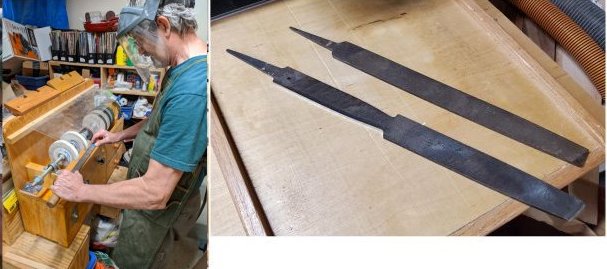
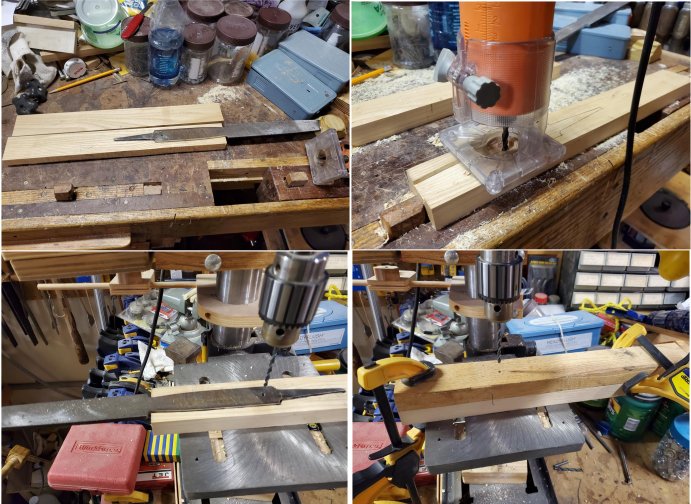
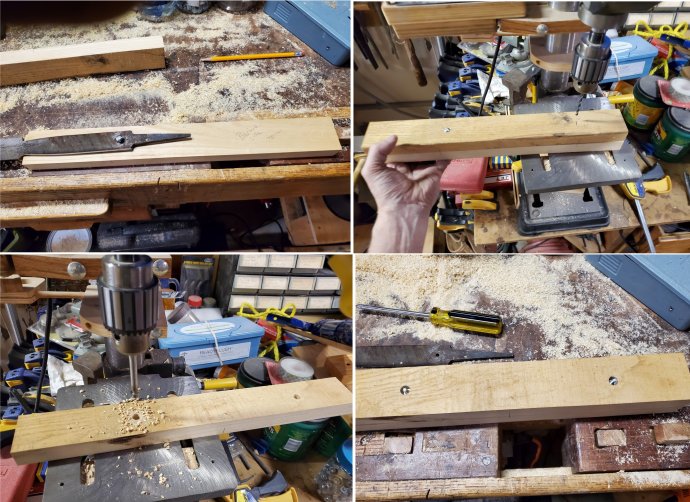
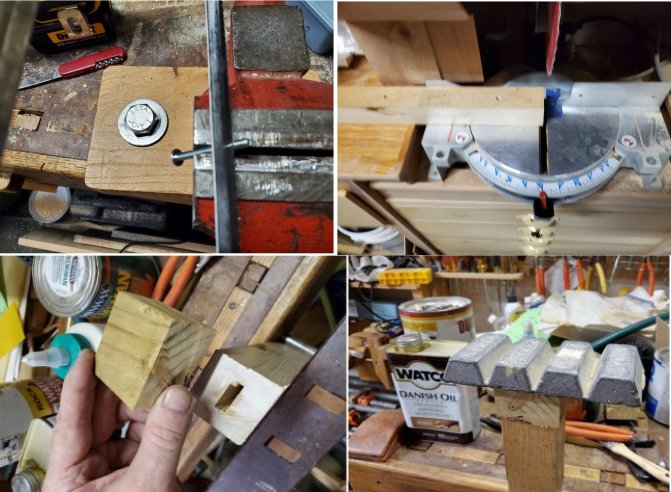
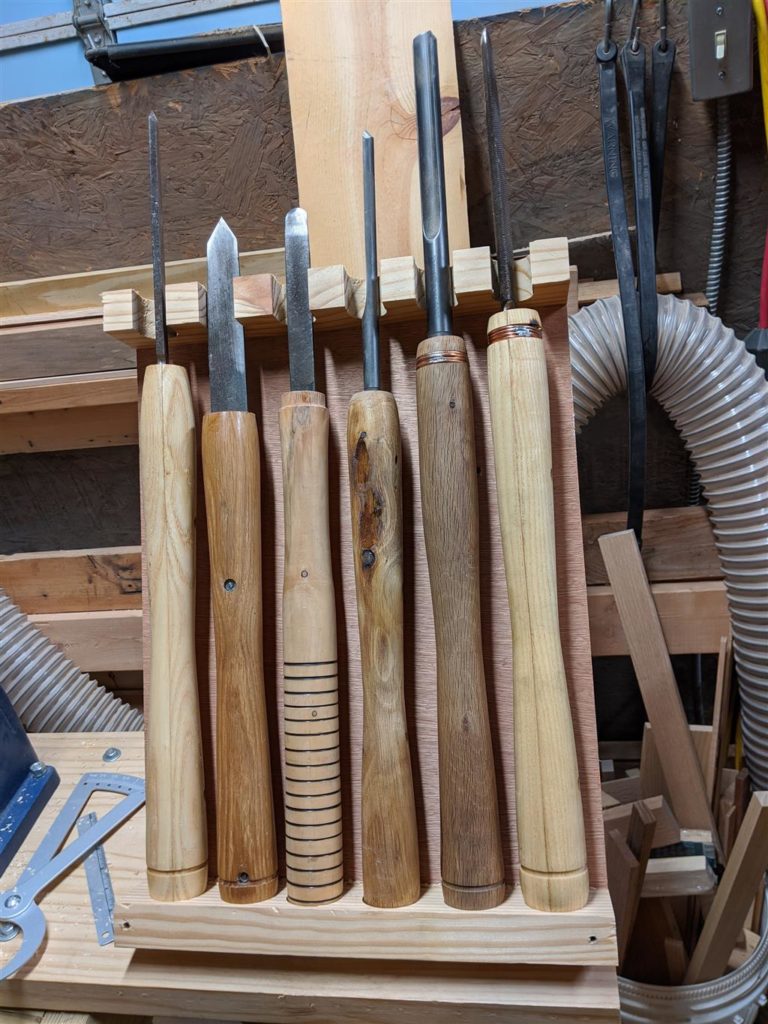
I wanted to make a separate power stand for my Shopsmith bandsaw and belt sander without changing the current Shopsmith operation.
I started with a stand made from 4×4’s with 2×4 cross members bolted together with lag bolts. I made the stand 30 inches tall before attaching the sub-base. The 4×4 were cut at a 10 degree compound angle top and bottom. The outside lengths and widths were 25 and 22 inches at the bottom and 13 and 10 inches at the top. Note the angled cleats attached to the legs for mounting the motor.
I used a 1/2 hp motor turning at 1725 rpm with capacitive start. The motor wiring should allow the shaft rotation to be changed to match your mounting requirements. The motor was mounted to a piece of 3/4 inch plywood which was secured to cleats mentioned above with 3/8 inch captured hex bolts. Two and 1/2 inch long slots in the plywood mounting base allowed the motor base to be moved up and down while attaching the pulley belt. Don’t finalize the stand dimensions until you have the motor you will be using in hand and can determine the amount of space it needs within the stand. I used a 48 inch twist lock V-belt. You can adjust the length of the belt by adding or removing links.
I made the sub-base and base out of 3/4 x 17 x 17 inch plywood. A 4 inch by 1.5 inch slot was cut to allow the drive belt to pass through. This was later enlarged (made wider) on the sub-base to allow lateral adjustment of the base to align with the motor pulley (this varies depending on which Shopsmith accessory is attached).
Next I made the accessory base out of 12 x 9 x 1 1/2 inch thick oak. I added a top layer of 4 x 12 x 3/4 inch persimmon on top of this to provide enough thickness to drill the requisite 1 1/4 inch diameter by 1 3/4 inch deep mounting holes for the accessory base to be inserted into.
I mounted a steel electrical switch box to the front of the plywood motor base and wired in a 15 amp decorator (rocker arm) switch. For safety a 3/4 inch faceplate was added to recess the switch surface to prevent it from being powered accidentally.
Now a thin piece of oak with a notch in the upper section was placed over the switch face. Finger pressure in the notch turns the switch on, and knee pressure will turn the switch off – allowing hands and eyes to be kept on the machine. The lower portion of the oak cover was laminated on the inside surface to reduce the amount of travel required to engage the lower portion of the rocker switch.
To further enclose the motor area under the stand, I made tip out drawers that fit between the legs on the sides. The rounded projection on the sides is for insertion of the two screws which are loosely fastened into the legs and about which the drawer pivots. I store different size pulleys and extra links for the drive belt in them.
Here you can see the drawers installed and opened. Gravity keeps the drawers closed. Light pressure on the bottom side of the drawer will cause them to pivot open.
The drive belt and pulley were enclosed to protect the user. The motor was enclosed on the back side to keep sawdust from getting into the motor. Several inches of space around the motor was left to allow air flow for cooling.
Front view of the Bandsaw. Other considerations: This stand was intended for the bandsaw or belt sander only. It is underpowered for the joiner. Pulley size selection determines the accessory speed. Recommended speeds for the bandsaw vary from about 750 to 1200 rpm. Belt sander from about 1150 to 1750. Consult the v-belt vendor for minimum recommended pulley size. See Pully Calc for help determining your pulley sizes.