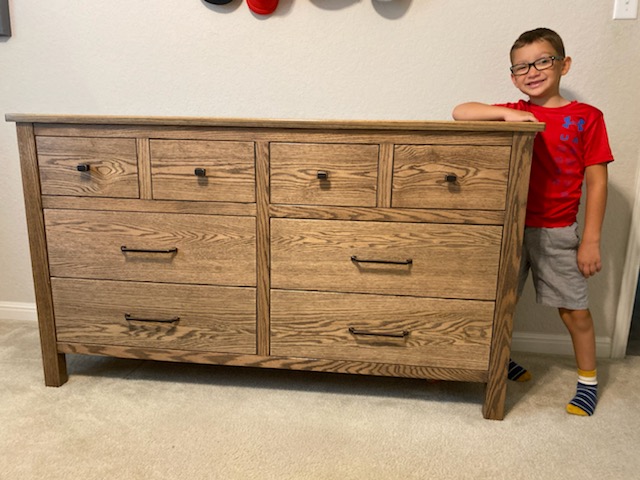
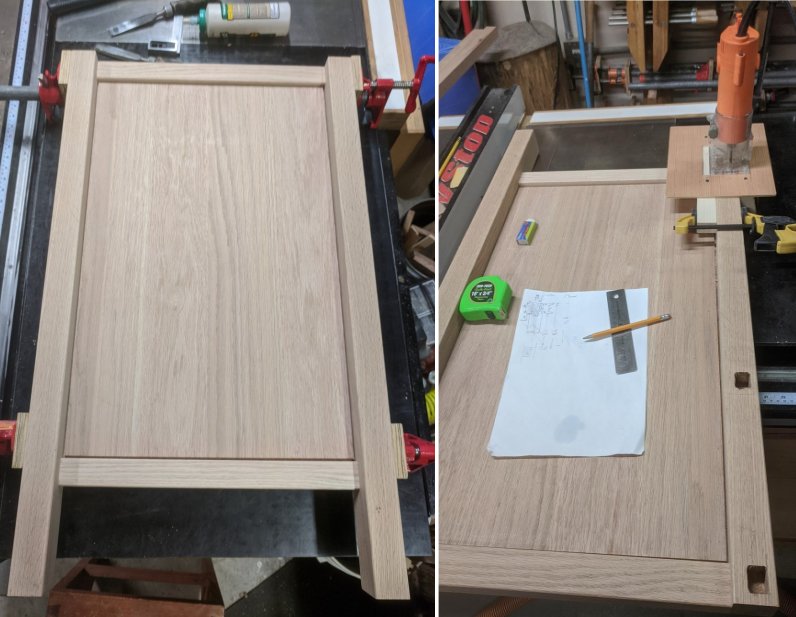
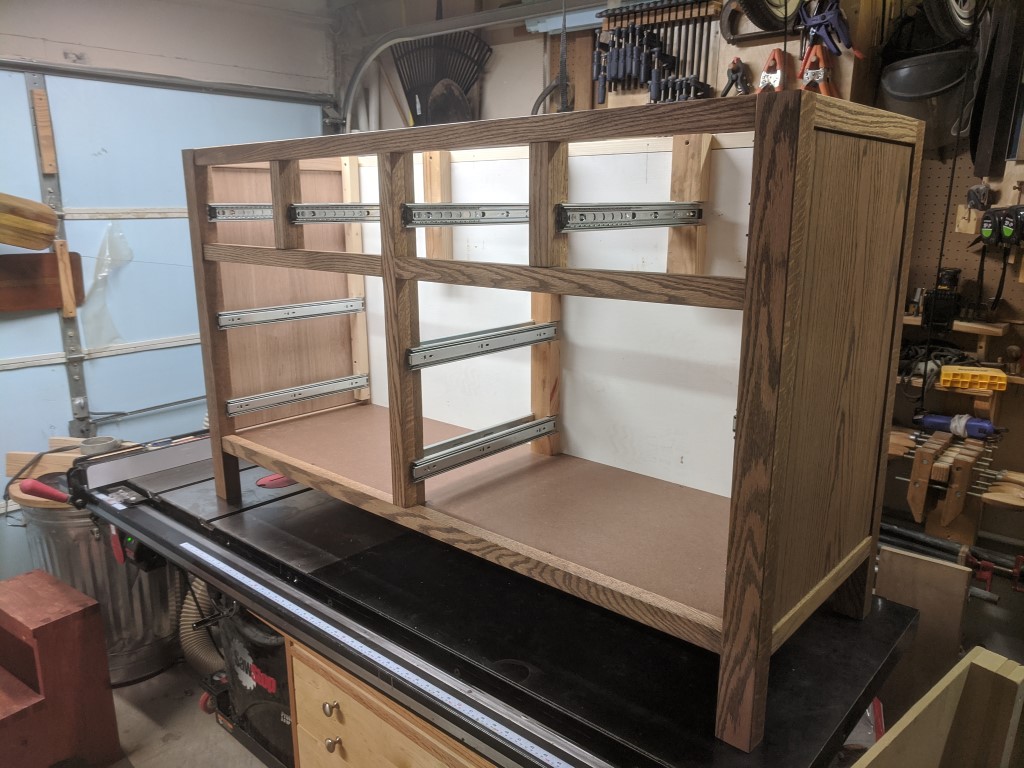
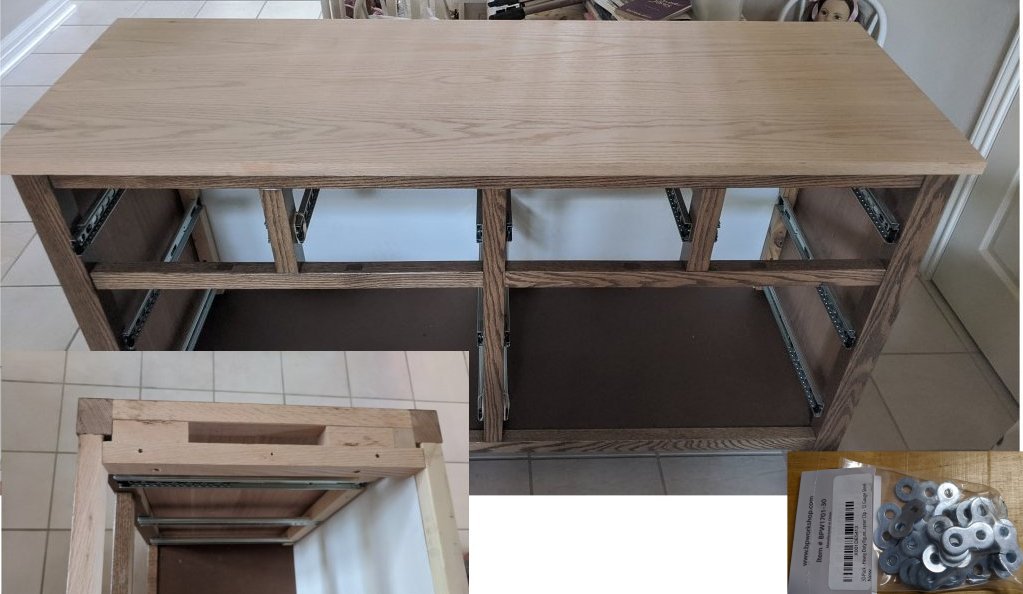
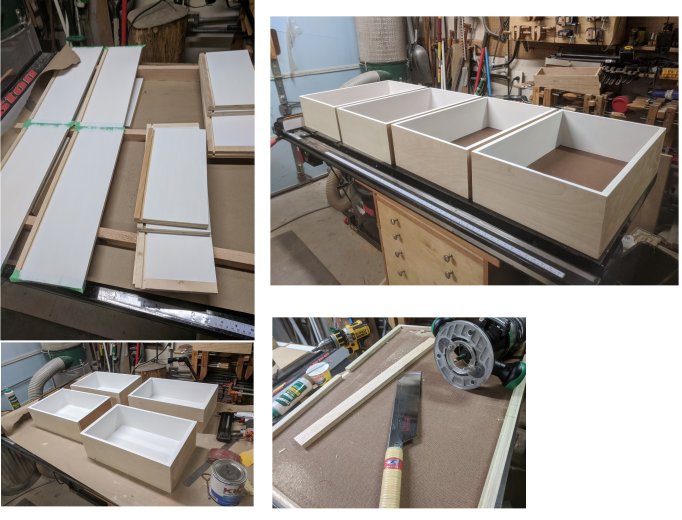
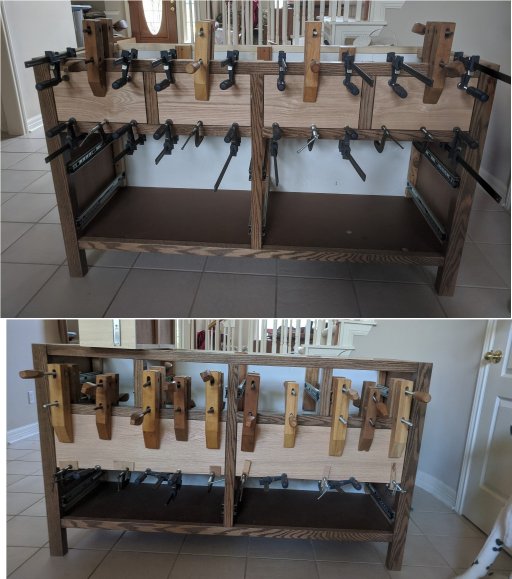
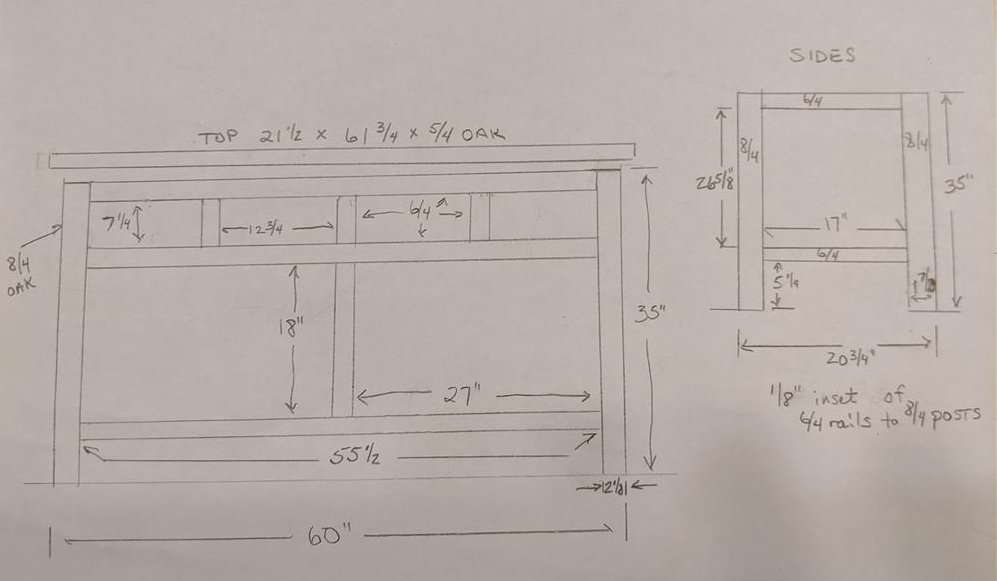
Daughters always find projects for Grandpa to do. This is the saga of a headboard for Levi. Originally she wanted to use reclaimed pallet lumber, but pulling rusted spiral nails out of pallets yielded diminishing returns. So I decided to use a 5 foot by 3 foot piece of 1/2 plywood as a substrate and attach contrasting wood species in a herring bone pattern. I started by laying out the pattern with pencil and square on the sized plywood sheet. I decided to make the board widths 3-1/8 inch wide to maximize some old redwood siding pieces I got from Grandpa Jake.
I started with the oak boards toward the middle of the piece. I carefully positioned the pieces using framing squares and clamps. The first row had to be right, since all the other rows would be aligned next to it. I used lead ingots to hold the boards down, and drilled and screwed up from the bottom side to secure the glued boards in place.
Each row was stained before being attached because some boards received a different stain than their neighbors. I found that was easier to drill the two pilot holes from the top of the plywood sheet before placing the boards because it was easier to determine where to place them. The whole assembly was elevated above the work surface so I could then counter-sink the holes and drive the screws in from below.
Here we are just over half done. Notice that the adjacent rows are different thickness to give the pattern some depth. I used a 45 deg chamfer bit in the router table to give a consistent edge. It also hides inconsistencies if any of the boards were not perfectly flat.
All board pieces were cut a little long so they hung over the edge. Before adding the pieces on the other side of the starting row, I trimmed all the boards on the just completed long side while I had the straight plywood edge on the other side to place against the table saw fence.
A 1-1/2 inch oak frame was added on the edges after completing the pattern. Glue was applied to the edges, then the oak boards were positioned to stand just a bit proud above the thickest boards in the herring bone pattern. Pipe clamps and brads were used to secure the trim until the glue dried overnight. Two coats of oil-based polyurethane were applied, with a light sand in-between coats. Wood species used in the pattern were oak, western red cedar, white pine (stained grey), redwood, and aromatic cedar.